Die Casting Injection Molding: Revolutionizing Metal Fabrication
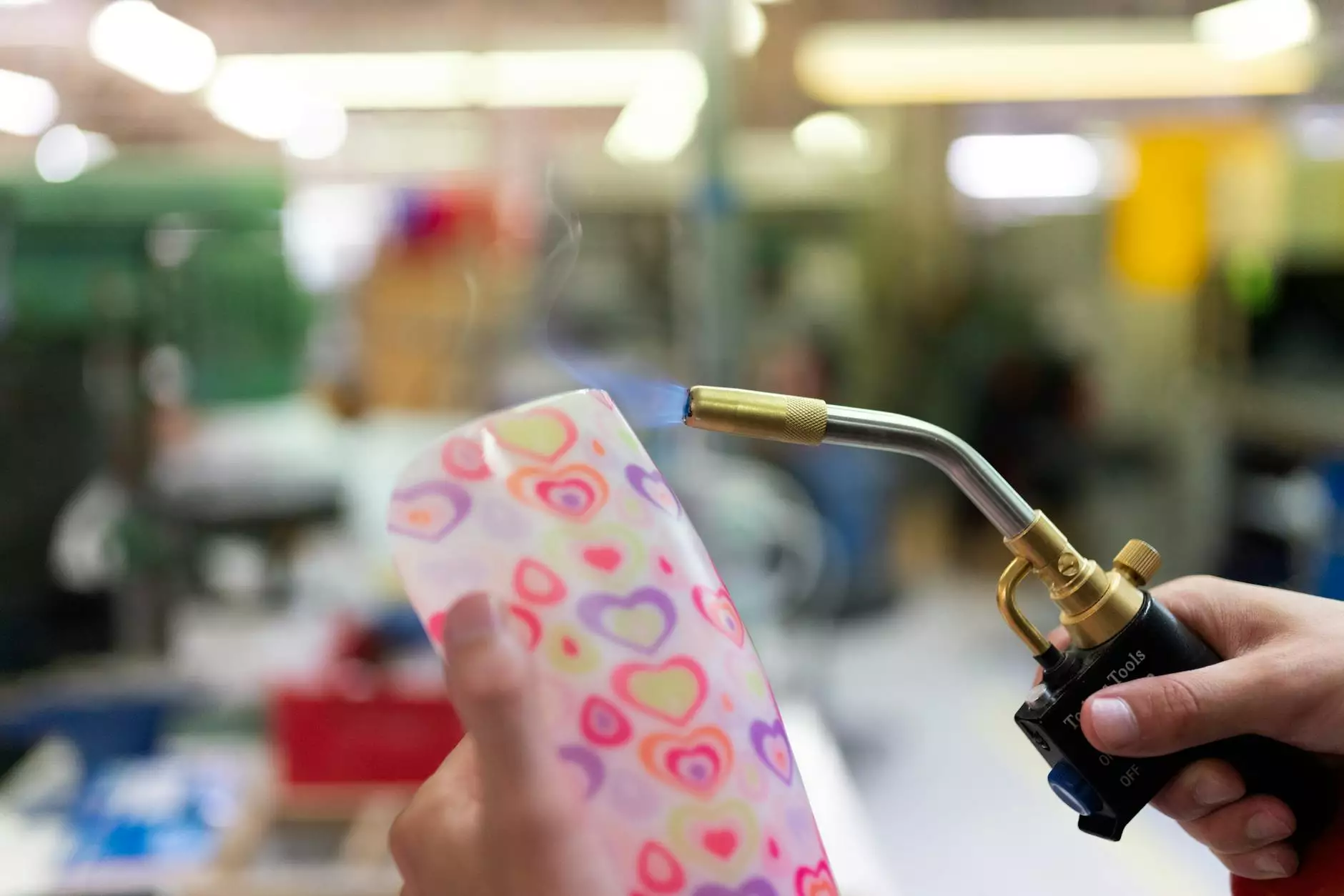
Die casting injection molding is swiftly becoming the gold standard in metal fabrication. This innovative process not only streamlines production but also provides unparalleled quality for manufacturers across various industries. With the surge in demand for precision-engineered components, understanding the intricacies of die casting and injection molding is essential for businesses looking to maintain a competitive edge.
The Fundamentals of Die Casting Injection Molding
At its core, die casting injection molding combines two highly efficient manufacturing processes: die casting and injection molding. Each technique has its own unique benefits, and when combined, they offer a robust solution for producing complex metal parts with intricate designs.
What is Die Casting?
Die casting is a metal casting process characterized by forcing molten metal under high pressure into a mold cavity. The key benefits of die casting include:
- High production rates: Die casting allows for the rapid production of thousands of parts in a short period.
- Complex geometries: It enables the creation of intricate shapes and designs that can be challenging to achieve with other methods.
- Excellent surface finish: Die-cast parts typically have high-quality surface finishes, reducing the need for secondary operations.
Understanding Injection Molding
Injection molding, on the other hand, is primarily used for plastics but can be adapted for metals in the context of die casting. This process involves injecting molten material into a mold to form the desired shape. Some advantages of injection molding include:
- Versatility: It can accommodate a wide range of materials, allowing for diverse product offerings.
- Low waste production: Injection molding leads to minimal material wastage, making it a cost-effective solution.
- Consistency and precision: Parts produced are highly precise, making it ideal for applications requiring uniformity.
The Synergy of Die Casting and Injection Molding
When combined, die casting injection molding creates a synergistic effect that enhances both processes’ strengths. This hybrid technique allows manufacturers to produce metal parts with complex features while maintaining speed and efficiency. Here are some compelling benefits of utilizing this process:
- Improved mechanical properties: The pressure used in die casting leads to denser and stronger parts.
- Enhanced design flexibility: Manufacturers can design parts that are not only strong but also lightweight, an essential requirement in industries like automotive and aerospace.
- Cost-effective tooling: Although the initial setup might be high, the long-term benefits of faster production times and reduced material waste make it an economical choice.
Industries Benefiting from Die Casting Injection Molding
Various industries have adopted die casting injection molding to enhance their manufacturing capabilities. Some of the most notable sectors include:
1. Automotive Industry
The automotive sector is one of the largest users of die casting technology. Components such as engine blocks, transmission cases, and other structural parts benefit from the strength and precision of die castings. This process enables automotive manufacturers to meet stringent safety and performance standards while reducing weight and enhancing fuel efficiency.
2. Aerospace Industry
In the aerospace industry, components must adhere to rigorous safety regulations and must be lightweight yet durable. Die casting injection molding offers the ability to produce complex parts that withstand extreme conditions. Parts like brackets, frames, and housings are often produced using this technique.
3. Electronics Sector
The electronics industry benefits from the high precision and surface finish of die cast components, which are critical for electronic housings and enclosures. These parts not only need to be aesthetically pleasing, but they must also provide reliable protection for sensitive electronic components.
Key Features of Die Casting Injection Molding
There are several key features that set die casting injection molding apart from other manufacturing processes:
1. Precision Engineering
The use of high-pressure techniques in die casting allows for extreme precision in manufacturing parts. Tolerances can often be kept within ±0.5mm, ensuring that each part produced matches its CAD specifications closely.
2. High Production Rates
With the capability of producing multiple components in a single shot, die casting injection molding significantly lowers labor and material costs. This efficiency is vital for companies requiring mass production.
3. Material Compatibility
Die casting typically utilizes non-ferrous metals such as aluminum, zinc, and magnesium. When combined with injection molding principles, it can also incorporate various alloys to meet specific mechanical and thermal requirements.
Future Trends in Die Casting Injection Molding
With advancements in technology, die casting injection molding is poised for significant evolution. Some of the emerging trends include:
1. Increased Automation
The move towards automation in manufacturing is evident. Smart technologies and robotics are being integrated into die casting processes, enhancing efficiency, reducing error rates, and improving safety.
2. Sustainability Focus
As businesses become more eco-conscious, the focus on sustainable manufacturing processes is critical. Die casting injection molding minimizes waste and can utilize recycled metals, appealing to environmentally responsible companies.
3. Advanced Materials Development
Researchers are continually developing new alloys and metal compositions that can withstand more extreme environments while maintaining lightweight properties. The future may see the introduction of new materials capable of operating in even more demanding applications.
Conclusion: Embracing the Future of Manufacturing
The integration of die casting injection molding into metal fabrication processes marks a pivotal moment in the industry. By adopting this innovative technique, manufacturers gain a considerable edge in producing high-quality, precise, and complex parts swiftly. As industries evolve, staying informed about advancements in die casting and injection molding will be crucial for businesses aiming to thrive in an increasingly competitive marketplace.
For businesses interested in exploring the advantages of die casting injection molding, contacting experts in the field is essential. At DeepMould.net, we specialize in providing cutting-edge metal fabrication solutions that align with our clients' needs, ensuring they remain at the forefront of their industries.